Человечество пребывало ещё в бронзовом веке, когда в различных регионах планеты уже создавали сплавы на основе железа.
Наступил железный век. Тысячелетиями усовершенствовались технологии литья чугунных орудий и различных механизмов, стальных клинков. Алхимики и химики выделяли из природных минералов металлические соединения и открывали новые металлы, возникла и развивалась металлургия – наука о производстве металлов.
С XVII века развернулась индустриализация. Для техники, новых видов транспорта, мостов, промышленных зданий потребовалось много металла, в первую очередь – высококачественной стали.
Эти задачи решали «методом проб и ошибок», а к концу XIX века – и на основе фундаментальных научных исследований. В металлургии, кроме химических процессов, для нагрева и плавления начали применять электрическую энергию.
Но темпы научно-технического прогресса продолжали расти. Во второй половине прошлого века создавались ракеты, атомные электростанции, суперистребители, мощные турбины, новые классы кораблей и многое другое, неизвестное и немыслимое. Техника нового поколения работала при сверхвысоких давлениях и ударах, невиданных ранее высоких и, наоборот, очень низких (криогенно стойких) температурах, а также при других экстремальных нагрузках.
Конечно, металлурги продолжали создавать новые специальные типы сталей. Например, для повышения жаропрочности добавили в сплав вольфрам, ванадий, молибден. Но сталь от этого становилась ещё тяжелее. А масса многих машин и аппаратов должна быть как можно меньше. Требовались сплавы прочнее стали, жаростойкие и криогенностойкие, нержавеющие и не растворяющиеся в агрессивных средах.
В первой половине прошлого века уже начали широко применять лёгкий металл - алюминий и его сплавы. И хотя прочность их была намного меньше, чем у стали, они очень пригодились для лёгких конструкций, таких ответственных, как самолёты и дирижабли, и даже некоторые корабли.
Алюминий и его сплавы не ржавеют и не разъедаются почти никакими кислотами, поэтому из них изготовляют химическое оборудование, различную утварь. В электротехнике чистый алюминий пригодился из-за хорошей электропроводимости, а сплав алюминия с кремнием обладает отличными литейными свойствами и из него отливают корпуса двигателей внутреннего сгорания для автомобилей и самолётов.
Но алюминиевые сплавы сравнительно легкоплавкие. Необходимо было найти металл и создать из него сплавы лучше и легче, чем сплавы из железа.
И такой металл нашёлся. Причём, если железная руда и бокситы (сырьё для алюминия) сконцентрированы в определённых залежах, то сырьё для металла, отвечающего требованиям научно-технического прогресса, оказалось буквально под ногами, в виде песка или в виде руды.
Вспомним, что земная поверхность состоит из соединений металлов и неметаллов, ими покрыто дно морей и океанов, они растворены в морской воде. Вот только выделить металл из его соединений бывает совсем не просто. И тысячелетний путь, пройденный человечеством в поисках металлургических технологий, часто не подходил для того, чтобы «добыть» новый металл и организовать его производство. Вот и над укрощением крайне необходимого для современной техники металла специалисты работают уже более двухсот лет.
Одним из «любимых» занятий химиков прошлых веков было определять состав «земель», попадавшихся под руку. В 1791 году англичанин У. Грегор, исследуя состав магнитного железистого песка с пляжа Корнуолла, выделил новую «землю» (оксид) неизвестного металла.
А через четыре года независимо от него немец Мартин Генрих Клапрот (1743—1817) открыл в минерале рутиле новый элемент. Немецкий исследователь отметил невозможность определения свойств нового элемента только по его оксиду и назвал его титаном – в честь стойких борцов с богами Олимпа из древнегреческой мифологии.
Немного ранее он же открыл металл, который назвал ураном. Клапрот установил, что рутил и «земля Трегора»— оксиды одного и того же химического элемента, за которым и осталось название «титан».
В свободном виде титан не встречается, но зато находится на 10-м месте по распространённости в природе: в рутиле, ильмените, перовските, титаните, других минералах и в морских глинистых отложениях.
Первый образец металлического титана удалось выделить из оксида в 1825 году химику Каролингского университета (Швеция) Йёнсу Якобу Берцелиусу (1779-1848). Однако его способ был настолько сложным, а сам титан оказался настолько химически активным, что никто не увидел перспективы в его применении.
Только спустя 100 лет голландцы А. ван Аркел и И. де Бур в 1925 году, применив технологию термического разложения паров йодида титана (TiI4), наконец получили чистый титан.
Этот йодидный способ применяют для получения небольших количеств титана очень высокой чистоты (до 99,99%). Титановую губку помещают в реторту и нагревают до 100 – 200°С; внутрь реторты вводят и разбивают ампулу с йодом, взаимодействующим с титаном по реакции Ti+2I2 → TiI4. (В принципе, можно применять и другие галогениды). Разложение TiI4 на Ti+2I2 и выделение титана происходит на титановых проволоках, натянутых в реторте, нагретых до 1300- 1400°С пропусканием тока.
Было установлено, что титан – лёгкий прочный металл серебристо-белого цвета. Температура его плавления 16600С, точка кипения 32600C. Металл существует в двух модификациях: α-Ti и β-Ti, плотность которых, соответственно, равна 4,505 и 4,32 г/см3. Между прочим, титановая пыль при температуре 4000С взрывается. Пожароопасна и титановая стружка.
Ряд особых физико-химических свойств титана, прежде всего высокая удельная прочность (отношение прочности к удельному весу), большая коррозионная стойкость во многих агрессивных средах, хорошая обрабатываемость давлением и другие ценные технологические свойства делают его.
Действительно, в середине прошлого века научно-технический прогресс без титана и его сплавов начал «пробуксовывать». И пришлось, не считаясь с затратами, искать способы промышленного производства важнейшего материала.
Естественно, что перво-наперво попробовали выплавить титан так, как выплавляют из железных руд чугун («Страна знаний», 2015, №8). Концентрат титановой руды начали плавить в смеси с древесным углём или антрацитом в электродуговой печи и получили шлак из окиси титана и различных примесей.
Но «отобрать» кислород у титана непросто, поэтому на втором этапе решили использовать более активный элемент – хлор.
В специальную печь, в нижней части которой нагревается угольная пластина при пропускании через неё электрического тока, загружают титановый шлак, а через фурмы задувают хлор. И при температуре 800-12500С образуются пары четырёххлористого титана, а также хлориды других примесей. Пары очищают от твёрдых частиц, охлаждают в конденсаторах, и получают жидкий четырёххлористый титан.
Экспериментаторы нашли и другие способы получения титана. Не будем их описывать подробно. Отметим только, что получить четырёххлористый титан можно в хлоратоpax непрерывного действия, в солевом расплаве, в кипящем слое.
А научную основу третьего этапа – термитные реакции заложил Николай Николаевич Бекетов (1827-1911) («Страна знаний», 2015 № 4).
Магниетермию выполняют в герметичных реакторах (ретортах) из нержавеющей стали, установленных в электрических печах сопротивления. Из реторты откачивают воздух, заполняют её инертным газом аргоном, заливают туда расплавленный магний и, постепенно, – жидкий четырёххлористый титан. Титан восстанавливается магнием по реакции TiCl4+2Mg=Ti+2MgCl2 с выделением большого количества тепла.
Необходимая по технологии температура 800-900°С поддерживается в реакторе дозированной подачей TiCl4. (Вместо магния иногда применяют натрий, и этот способ восстановления называют натриетермическим.) Правда, к сожалению, получается не плотный слиток, а пористая титановая губка (до 60% Ti). С подобной железной заготовкой – «крицей» имели дело металлурги-кузнецы в древности. («Страна знаний», 2015, № 8).
К сожалению, при проковке этой губки чистый титан получать не удавалось. Необходимо было разрабатывать ещё одну технологическую операцию – переплавлять эту смесь так, чтобы избавить её от примесей.
И здесь наступил следующий этап «борьбы человека с титаном». Теперь из губчатого титана требовалось выплавить плотные, без пор и включений металлические заготовки для проката или отливок. В середине ХХ века перед мировой металлургией открылся очередной этап покорения своенравного металла – придание ему нужных для новой техники качеств.
Результаты работ засекречивали: основными заказчиками были творцы новой военной техники. Решением задач переплава и сварки в принципе и применительно к конкретному производству занимались десятки институтов и лабораторий в СССР, США, Великобритании, Франции и ещё в некоторых странах. Работали интенсивно – гонка вооружений уже набрала обороты.
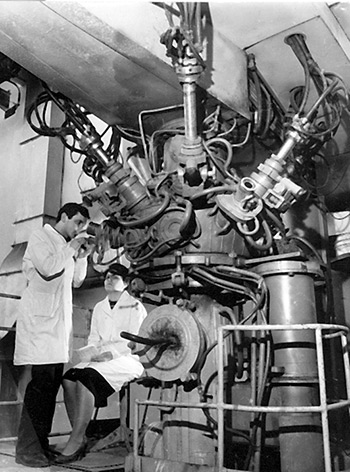
в ИЭС им. Е.О.Патона
Работы по исследованию и разработке металлургических и сварочных процессов применительно к титану были начаты в Институте электросварки им. Е.О. Патона (ИЭС) НАН Украины в конце 50-х годов прошлого века под общим руководством академика Бориса Евгеньевича Патона (род. 1918).
Вскоре в Киеве впервые в мире были разработаны самые эффективные технологии получения слитков титана и его сплавов из первичной шихты и из вторичных отходов. Для решения проблемы пригодились знания, накопленные в процессе создания новых сварочных технологий и электрошлакового переплава.
Сотрудники ИЭС им. Е.О. Патона применили энергию электронных лучей, дуговой плазмы, индукционный и электрошлаковый нагрев. Каждый из процессов имеет свои преимущества и используется для производства металла с конкретными свойствами, именно такими, какие требуются для ответственных конструкций.
Мощный электронный луч плавит заготовки в вакууме под давлением 0,01- 0,1 Па. Технологические процессы обеспечивают удаление посторонних примесей и растворённого газа, позволяют получать слитки титана и его сплавов с однородной бездефектной структурой. Для их внедрения было создано семейство многоцелевых промышленных плавильных электронно-лучевых установок (ЭЛУ).
В плазменно-дуговых электропечах заготовки расплавляют одним или несколькими дугами, сжатыми потоками аргона в плазмотронах. Плазменно-дуговая печь позволяет выплавлять титановые слитки непосредственно из кусковой шихты (губчатого титана), минуя операцию прессования заготовок.
Одним из наиболее универсальных независимых источников нагрева является высокочастотное магнитное поле, создаваемое электрическим током в индукторе. Особенности индукционного нагрева, в том числе интенсивное перемешивание жидкого металла, гарантируют выравнивание химического состава, возможность выдерживать металл в жидком состоянии неограниченное время в вакууме, обеспечивают высокое качество отливок.
Альтернативой переплаву в вакуумных условиях является электрошлаковый переплав. Для него не требуется такого сложного оборудования, строгого выдерживания режима плавки, и при достаточно высоком качестве себестоимость работ самая низкая. Наилучшего качества удаётся достичь в печах камерного типа.
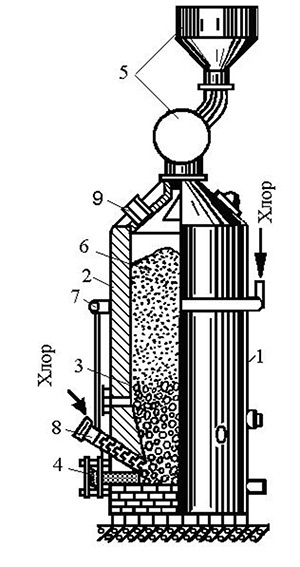
четырёххлористого титана:
1 – корпус печи;
2 – футеровка;
3 – угольная набойка;
4 – токоподводящие графитовые
электроды;
5– устройство загрузки шихты;
6 – брикетная шихта;
7, 8 –трубки для подачи хлора;
9 – отверстие для удаления
парогазовой смеси.
В ИЭС была разработана технология магнитоуправляемой электрошлаковой плавки для производства сплавов титана с любым большим количеством компонентов. Наиболее существенными преимуществами этой технологии являются возможность рафинирования низкосортного дешёвого сырья от вредных примесей, высокая плотность литья, меньшие затраты технологической электроэнергии и сравнительно дешёвое оборудование.
И чем дешевле становилось производство титана и сплавов с качествами, необходимыми для ответственных изделий, тем больше была в них потребность. Только в СССР за короткое время производство титановой продукции было налажено на двух десятках заводов.
Для экономии дорогого металла в тех конструкциях, где требовалась стойкость к агрессивным средам, но не важен был вес изделия, были разработаны способы изготавливать биметалл. В 1980-х годах было освоено производство биметаллических листов путём горячей прокатки заготовок. И самым лучшим конструкционным материалом является композиция сталь+титан, т.е. сталь, плакированная (покрытая) титаном.
В ИЭС им. Е.О. Патона открыт цех «Титан», который может выпускать до 1500 т титановых слитков в год для проката высококачественных полуфабрикатов.
Так, из таких сплавов толщиной 200-250 мм на Феодосийском судостроительном заводе «Море» были изготовлены крыльевые устройства для морских судов. В 2009 году была создана технология электронно-лучевой плавки крупногабаритных слитков жаропрочных сплавов на основе титана.
Впервые в мире получен слиток диаметром 840 мм из жаропрочного титанового сплава ВТ3-1, а вскоре был получен слиток диаметром 1100 мм, длиной до 4000 мм, массой 16 тонн.
Впервые в мировой практике в цехе «Титан» спроектирована, изготовлена и запущена в эксплуатацию электронно-лучевая установка для получения титановых слитков недроблёных блоков губчатого титана. Для изготовления атомных и химических реакторов ИЭС им. Е.О. Патона налажено производство полых слитков, из которых раскатывают титановые кольца диаметром до 2000 мм.
Впервые в мире были изготовлены бесшовные титановые трубы длиной до 9000 мм из трубной заготовки.
Всё большее применение в гражданских отраслях промышленности находят как традиционные титановые сплавы, так и новые титановые сплавы с уникальными физико-химическими характеристиками. Титан является одним из наиболее распространённых геттерных (от «геттер» — газопоглотитель, вещество, поглощающее и прочно удерживающее газы, кроме инертных) материалов, используемых в высоковакуумных насосах.
Детальное изучение коррозийной стойкости сплава Т100 в разнообразных агрессивных средах, в том числе и в биологических, показало его перспективность для применения в медицине для изготовления эндопротезов и медицинских инструментов.
Для потребностей стоматологии в ИЭС им. Е.О. Патона разработан титановый сплав системы Ti-Al-Nb-Zr.
Одним из важнейших потребителей титановых сплавов в Украине является аэрокосмический комплекс. В конструкциях самолётов масса деталей из титановых сплавов составляет 8 – 9 % массы планёра. Это, главным образом, тяжело нагруженные силовые элементы, такие как подкосы и цилиндры шасси, кронштейны системы управления, детали механизации крыла, противопожарные перегородки, грузовые дорожки настила.
Из титановых сплавов изготавливают трубопроводы, теплообменники, компенсаторы и другие узлы самолетов.
В химической, пищевой промышленности из сплавов титана делают реакторы, трубопроводы, насосы, трубопроводную арматуру, опреснительные установки и др.
Первой в мировой практике монументальной скульптурой из титана является памятник Юрию Гагарину на площади его имени в Москве.
Титановые сплавы имеют наиболее высокую удельную прочность среди всех металлических материалов. Титан используют для легирования сталей и создания спецсплавов. Разработано множество сплавов титана с различными металлами. Нитинол (никель-титан) — сплав, обладающий памятью формы, применяется в медицине и технике.
Алюминиды титана являются очень стойкими к окислению и жаропрочными. Карбид, диборид, карбонитрид титана — важные компоненты сверхтвёрдых материалов для обработки металлов.
Титановые сплавы используются при изготовлении спортивных товаров, мобильных телефонов, часов, бронежилетов.
На любые металлы, керамику, стекло и многие другие материалы можно напылить нитрид титана, который имеет цвет золота, но, в отличие от него, это тончайшее покрытие очень прочное и во много раз дешевле. Технология напыления разработана в Физико-техническом институте в Харькове и широко применяется для покрытия металлом инструментов, зубных коронок, посуды, куполов церквей и изделий бижутерии.
Крупнейшими в мире сварными конструкциями из титановых сплавов являются малошумные тяжёлые ракетные подводные крейсера стратегического назначения (ТРКСН проекта 941, шифр «Акула», по классификации НАТО – «Typhoon»). Первый из 12 кораблей был построен в Северодвинске на «Севморзаводе» в сентябре 1979 года по технологиям, разработанным в ИЭС им. Е.О. Патона.
Нигде в мире больше нет подводных кораблей водоизмещением 28500 т, длиной 172,8м, шириной 23,3м. Этот крейсер может погружаться на глубину 500 м и идти там со скоростью 27 узлов. Конструкция ТРКСН выполнена по типу катамарана из двух раздельных прочных корпусов (диаметр каждого 7,2 м), между которыми расположены отсеки управления, торпедный и ракетный.
Использование титановых сплавов позволило уменьшить массу корпуса, увеличить глубину погружения, уменьшить магнитное поле. Конечно, и в странах НАТО имеются титановые лодки, но их тактико-технических данные хуже.
Несмотря на явные успехи в покорении титана, учёные продолжают совершенствовать его производство, а конструкторы и инженеры – создавать новую технику.
Сейчас мировое производство титана составляет около 4,5 млн т. в год. При нынешних темпах его потребления мировых разведанных запасов титана хватит более, чем на 150 лет.
А.П. Лютый, кандидат технических наук, завод «Днепроспецсталь», г. Запорожье